As the Mahoning Valley’s economy continues to struggle following the collapse of the local steel industry, interest in collaborative and cooperative economic models has grown as a way to reverse decline. Roy Messing of the Kent State University Ohio Employee Ownership Center shares the history of efforts to create employee-owned cooperatives in response to the loss of manufacturing jobs in the region. —Quilian Riano, In the Mahoning Valley chief editor
Explore these related features: Read more about the future of work in the region in a profile of Building a Better Warren. Learn how the philanthropic sector is working to create an equitable and just economic future for the Valley in an interview with Jennifer Roller, president of the Wean Foundation.
The idea of employee ownership (EO) first entered the conversation in the Mahoning Valley in the late 1970s, as it was proposed as a way forward for a steel production company that was facing closure due to fierce competition from subsidized foreign operations. In the years since, some Mahoning Valley EO steel-related companies flourished, while others continued to struggle. In recent decades, new interest in EO has come from enterprises outside the steel industry. Given the recent economic trauma brought on by the COVID-19 pandemic, can EO once again be a model to move the local economy forward to financial sustainability?
Background
The shuttering of General Motors’ Lordstown Plant in March 2019 delivered one more blow to the Mahoning Valley community, which has suffered long-term economic decline since the late 1970s. The valley’s economic fortunes had long been associated with the fate of the steel industry. The region’s initial economic growth in the early nineteenth century was tied to its large deposits of both coal and iron ore. Once the local steel industry was established, it was well located to process iron ore deposits being mined throughout the Great Lakes basin. The area’s steel output continued to grow through World War II.
Unfortunately, the Mahoning Valley failed to diversify its economic base over time. The result was that the area’s aging steel mills lacked proper reinvestment and became uncompetitive. The “dumping” of foreign-produced steel on the US market starting in the late 1970s undercut the ability to compete profitably. Youngstown Steel and Tube Company, which had become a subsidiary of New Orleans–based Lykes Corporation in 1969, closed the bulk of its Campbell, Ohio, production in September 1977, resulting in the layoff of some 5,000 workers. Known as Black Monday, this event marked the beginning of the region’s decline. US Steel and Republic Steel subsequently shuttered their local operations in quick succession. The lack of local ownership and decision-making played a significant role in the above closures, as corporate leaders felt little responsibility to their employees or the Youngstown–Warren region. These closures ultimately led to the loss of more than 40,000 jobs in the area, as manufacturing firms and companies that were connected to these steel productions facilities followed suit.
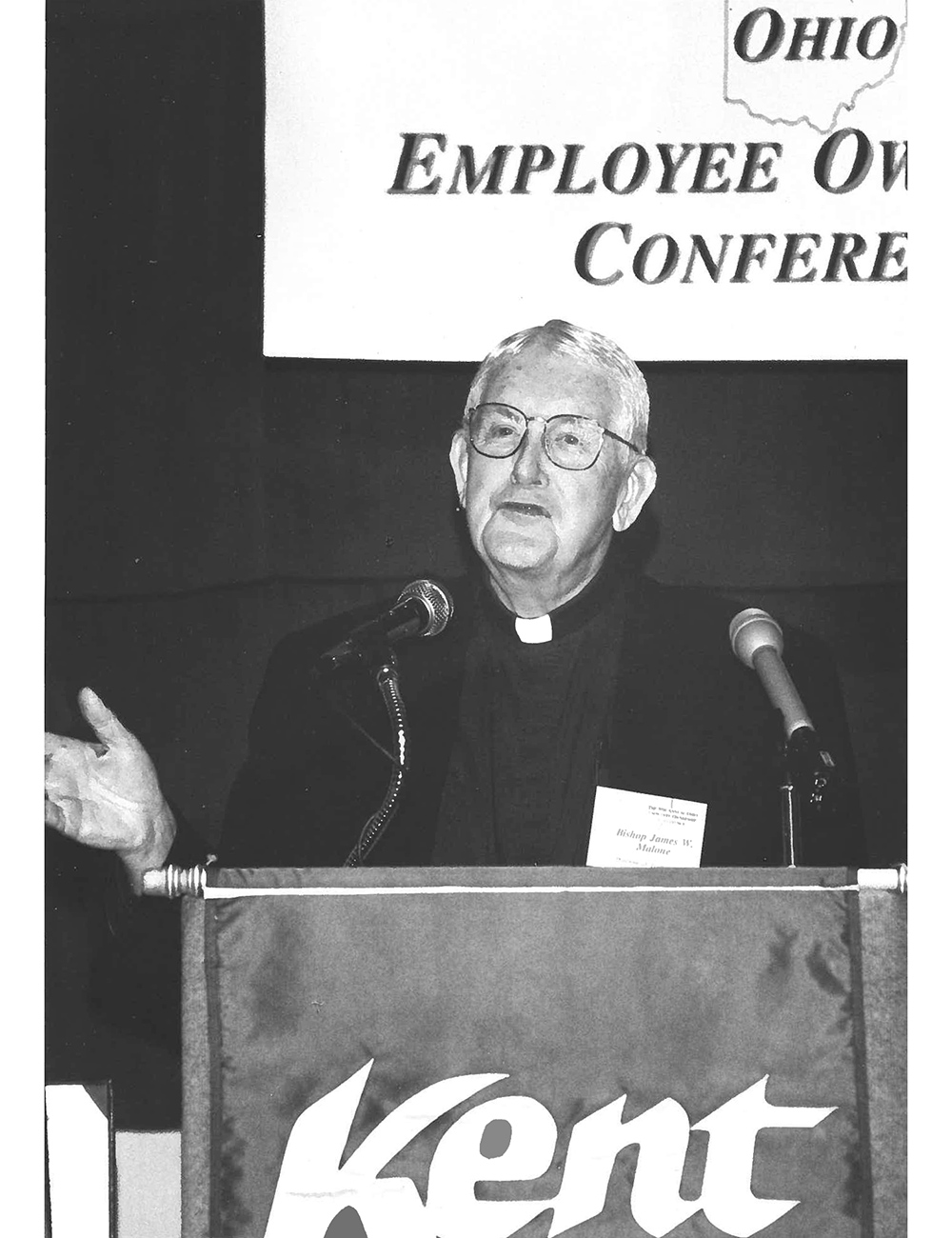
Bishop James W. Malone of the Diocese of Youngstown, Ohio, in 1996, speaking at the 11th annual Kent State University Ohio Employee Ownership Conference. Credit: Kent State University Ohio Employee Ownership Center
The Ecumenical Coalition: Vision on a Grand Scale
In response to the dire economic conditions facing the community, Bishop James W. Malone of the Catholic Diocese of Youngstown and Bishop John H. Burt of the Episcopal Diocese of Ohio convened a meeting of local religious leaders in September 1977 to address the impact of steel facility closures. This resulted in a coalition of over 200 local religious leaders focusing on the needs of the community. Bishop Malone became an active supporter of EO. The coalition proposed that the workers and the community become owners and reopen the old Youngstown Steel and Tube Campbell facility. The ecumenical coalition led a “Save Our Valley Campaign” that included the development of “Save Our Valley Accounts” at local banks. This effort gained wide community support, displaying the region’s commitment to restarting the steel facility under new local ownership.
The first step to make the project a reality was to complete an initial assessment of the feasibility of worker/community ownership and operation of the Campbell facility. This initial study outlined a reasonable chance of project success. Civic and area leaders came together as the Mahoning Valley Economic Development Committee to further study the project and implement a plant-reopening plan should it meet all the necessary approvals. The United States Department of Housing and Urban Development provided additional funding to further develop a plan that outlined the cost to upgrade, restart, and operate the facility ($450 to $700 million over the next five years).
Unfortunately for the local community, capital was never obtained. Neither steel production nor the corresponding jobs returned to the Campbell facility.
A Renewed Interest in Employee Ownership
While the Campbell facility did not become employee-owned in the late 1970s, several companies in the steel industry embraced this ownership model in the 1980s and 90s. Efforts by the Ohio Employee Ownership Center (OEOC) and other community/economic development organizations to avoid plant shutdowns or restart shuttered plants provided guidance and resources that allowed steel production in some form to continue in the region. Five companies in or with close ties to the steel industry became, in part, employee-owned near the end of the century.
- 1987: Bliss-Salem Inc., Salem, OH
- 1993: McDonald Steel Corp., McDonald, OH
- 1995: Sharpsville Products, Sharpsville, PA
- 1997: Falcon Foundry, Lowellville, OH
- 1998: Brainard Rivet, Girard, OH
Of the companies listed above, only Falcon Foundry had an EO formation that wasn’t associated with a restart or new formation from a bankrupt or shuttered facility (often a former division of a corporate conglomerate). The OEOC and other similar groups focused on retaining or “regaining” jobs lost to plant closures through the creation of locally and/or employee-owned entities. EO made it possible for these enterprises to move forward with operations with additional funding attained to organize under the employee ownership model.
In the case of Brainard Rivet, operations ceased at one point, with the plant shuttered for ten months. However, this closure wasn’t due to a lack of profits; instead, the parent company wanted to move the operation to a less labor-friendly climate in Virginia. Civic, religious, and government leaders got involved in supporting the cause of reopening. The Ohio governor’s office also engaged in the effort. Ultimately Fastener Industries, an employee-owned Cleveland area company, acquired the Girard, Ohio, operation, and it became a new division of the organization. The local employees received the same benefits as those employed by the parent organization.
McDonald Steel, Falcon Foundry, and Brainard Rivet still benefit from employee ownership today. Unfortunately, Bliss-Salem and Sharpsville Products, while initially successful under an EO structure, were unable to weather the storm of subsidized foreign steel competition, and their operations had to be shuttered and sold off at subsequent dates.
The First 20 Years of the Twenty-First Century
There has been limited expansion of EO in the Mahoning Valley since the turn of the century.
While there has still been a significant focus and effort to save jobs and companies in the steel industry and related fields during this period, steel’s long-term decline and less-than-stellar financial outlook made the task of restructuring these businesses for a successful future too burdensome for EO.
A handful of mission-based worker cooperatives were started in the region; they ultimately ceased due to limited outside support and challenging business circumstances.
There have been a few successful transitions of privately owned businesses to some level of employee ownership during this period. The two companies that moved to an EO model during this timeframe both did so as part of a long-term “succession plan” as their owners moved towards their retirement years. In 2006, Fireline, Inc., which specializes in refractory products and ceramics, formed an Employee Stock Ownership Plan (ESOP) for its employees. Five years later, Grand River Rubber & Plastics of Ashtabula formed an ESOP for its employees.
These new employee-owned companies, combined with those that formed in the 1990s, bring the total number of employee owners in the Mahoning Valley region to about 500.
Opportunities for Employee Ownership in the 2020s
At the beginning of 2020, many of us in the “Exit Planning” community believed that the largest threat to small and medium-sized business in America was the wave of aging baby-boomer business owners progressing towards retirement without adequate plans to exit their enterprises. Many professionals believed that this was an opportunity to continue some of these businesses under an EO structure.
Then the Covid-19 virus emerged; its impact has been profound. The large-scale shut down of the economy in order to slow the spread of the virus led to US unemployment rates skyrocketing from historic lows to more than 15 percent—a higher unemployment level than at any time during the Great Recession—in a matter of a few months. Many of the small- and medium-sized enterprises that were idled were forced to make agonizing decisions about the future of their organizations: reinvest much of their life savings (and perhaps take on additional debt) to restart or recast their enterprise’s future in this still uncertain time, or cut their losses and forgo reopening the business, even though it may have been a viable long-term entity. Either way, there was a negative impact on many business owners and their workers who have helped create and sustain the economy in communities like the Mahoning Valley.
While establishing EO for large corporations hasn’t happened to date in this region, the model has been successfully deployed in small- and medium-sized businesses. Many lessons have been learned in the 40-plus year journey of exploring and expanding EO. We need to study these lessons, assess the situation with local businesses, determine when ownership by employees is the right solution, and apply all of our knowledge and experiences to move these companies—of which many will be financially stressed even in periods of economic health—forward toward sustainable, worker-owned futures.
Biographies
is the director of state center operations for the Employee Ownership Expansion Network where he supports the efforts of local groups that launch and seek to sustain employee ownership centers in states where they previously did not exist. He engages a wide range of business support groups in these states to build business owner awareness of the option to transition ownership to employees as an exit or retirement strategy. For the past eight years he was the director of the Kent State University Ohio Employee Ownership Center, an outreach center that supports businesses in three primary areas: business exit/succession planning, assisting prospective and existing employee-owned companies, and leading the development of employee-owned and other cooperatives. The center has a long history of supporting the development of employee stock ownership plans and, more recently, employee/worker-owned cooperatives at a variety of levels through its business exit/succession planning activities.
The views expressed here are those of the authors only and do not reflect the position of The Architectural League of New York.