A Fresh Take on Low-Carbon Construction
Katie MacDonald and Kyle Schumann’s Exhibit Columbus installation uses innovative technology to deploy climate-friendly materials.
October 13, 2023
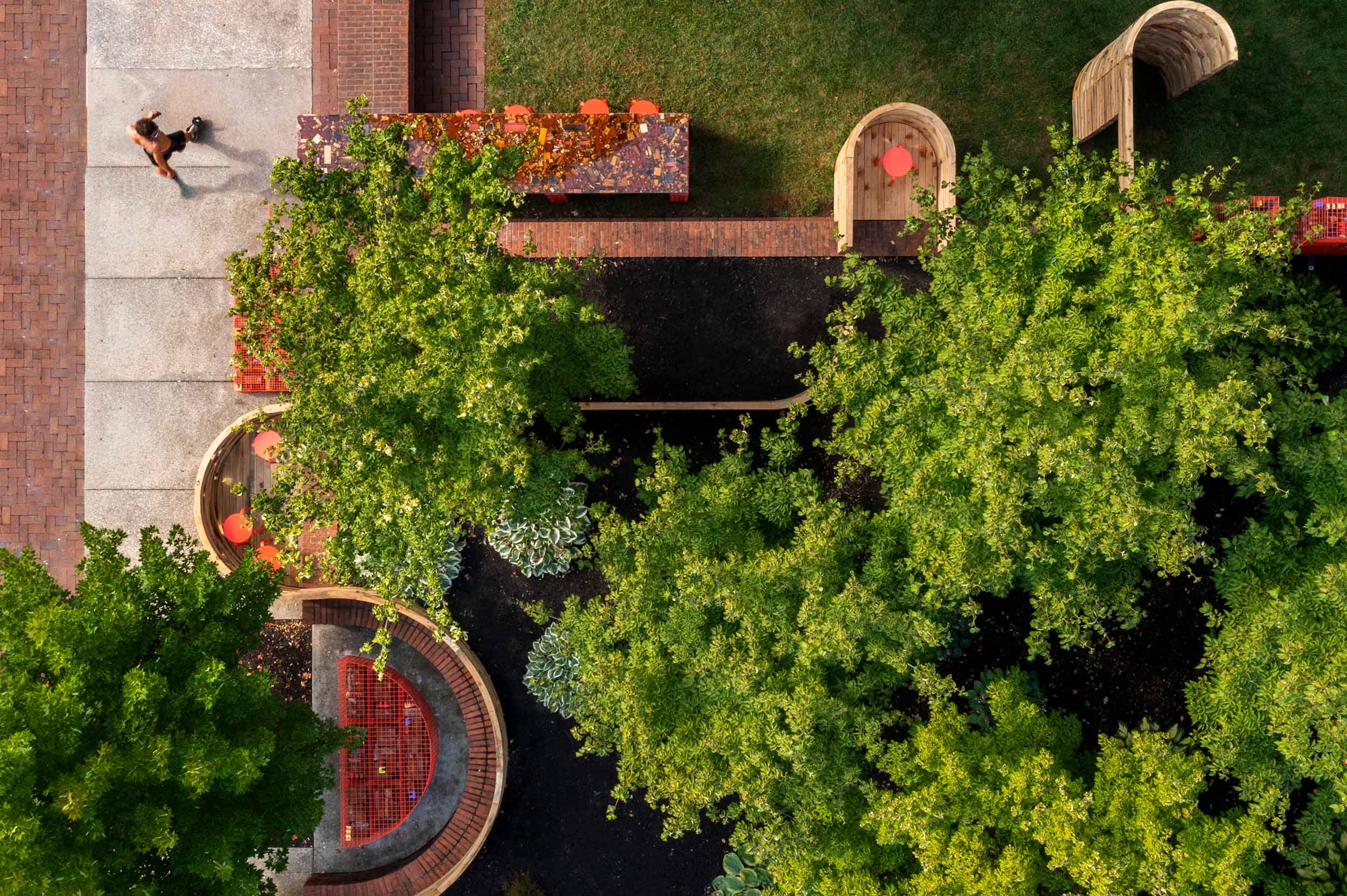
After Architecture’s Sylvan Scrapple installation at the 2023 Exhibit Columbus exhibition in Columbus, Indiana. Image credit: Hadley Fruits
After Architecture is a 2023 League Prize winner.
What can you build from waste materials like salvaged bricks or trees downed by a storm—and how might you standardize that process? This question underlay the design of After Architecture’s 2023 Exhibit Columbus installation, Sylvan Scrapple.
For the practice’s founders, Katie MacDonald and Kyle Schumann, the project is part of an ongoing body of research exploring nontraditional building materials in search of low-carbon options that can be deployed at scale.
The League’s Anne Carlisle and Sarah Wesseler spoke with MacDonald and Schumann as they wrapped up their work on Sylvan Scrapple, which is on view in Columbus, Indiana, through November 26.
*
Anne Carlisle: Tell us about your Exhibit Columbus installation.
Katie MacDonald: Sure. The project brings our approach to material resourcefulness to Columbus, looking at two different local material streams: one from Indiana and one from Virginia.
In Indiana, we’re working with bricks that were salvaged from the Irwin Block, a historic Queen Anne–style building in Columbus that burned down last December. We’re reconstituting the bricks into gabion cages that form a series of urban furniture: wall, dining table, coffee table, and stairs.
The second material stream is nonlinear wood sourced here in Virginia, which we’re using to construct a system of both straight and curved walls. These walls form a single line that snakes across the project site, interacting with existing landscape elements and forming a variety of intimate spaces to sit, eat, rest, and gather. The wood is sourced from trees felled during a historic winter storm in January 2022.
While there’s a long history of producing linear wood through sawmilling into straight lumber, our project looks at how you can respond to the natural curvature of species that don’t grow tall and straight, leveraging these geometries within the design assembly for their formal and structural potentials.
Kyle Schumann: Working with nonlinear wood has required us to develop a new fabrication technology. This is characteristic of our recent work: rethinking the manufacturing of materials. There are a lot of biases built into the tools we use—woodworking tools like the table saw assume a rectilinear board, for example. So working with faculty in environmental science and mechanical engineering here at the University of Virginia, we built a robotic sawmill that allows us to digitally model and then execute complex three-dimensional cuts that curve or twist along nonlinear logs.
Another aspect of the project relates to this year’s Exhibit Columbus theme, which is Public by Design—it’s focused on activating downtown and engaging with the public in the design process. So we put out a public call for recipes that engage with food waste in some way, with the goal of enhancing the material narrative of the installation, tying back to the brick reuse narrative and also tying together food and architecture. We think there’s a parallel understanding between the two: everybody eats, everybody interacts with buildings.
We asked the public to provide a recipe using food waste, and also to share an image of that plated meal on a place setting, using objects from their home. It’s a way to think about materials and reuse, but also about design aesthetics. The home and meals are such personal things: You can start to understand people through the objects they bring to their table. Those contributions from the public will be presented with the installation through an exhibition, entitled Table Scraps, of a series of placemats that are printed with the place-setting images and recipes.
MacDonald: One of the physical design elements that anchors the installation is a fifteen-foot-long table, and the goal is that discussions about food and buildings, informal meals, and community gatherings can happen there.
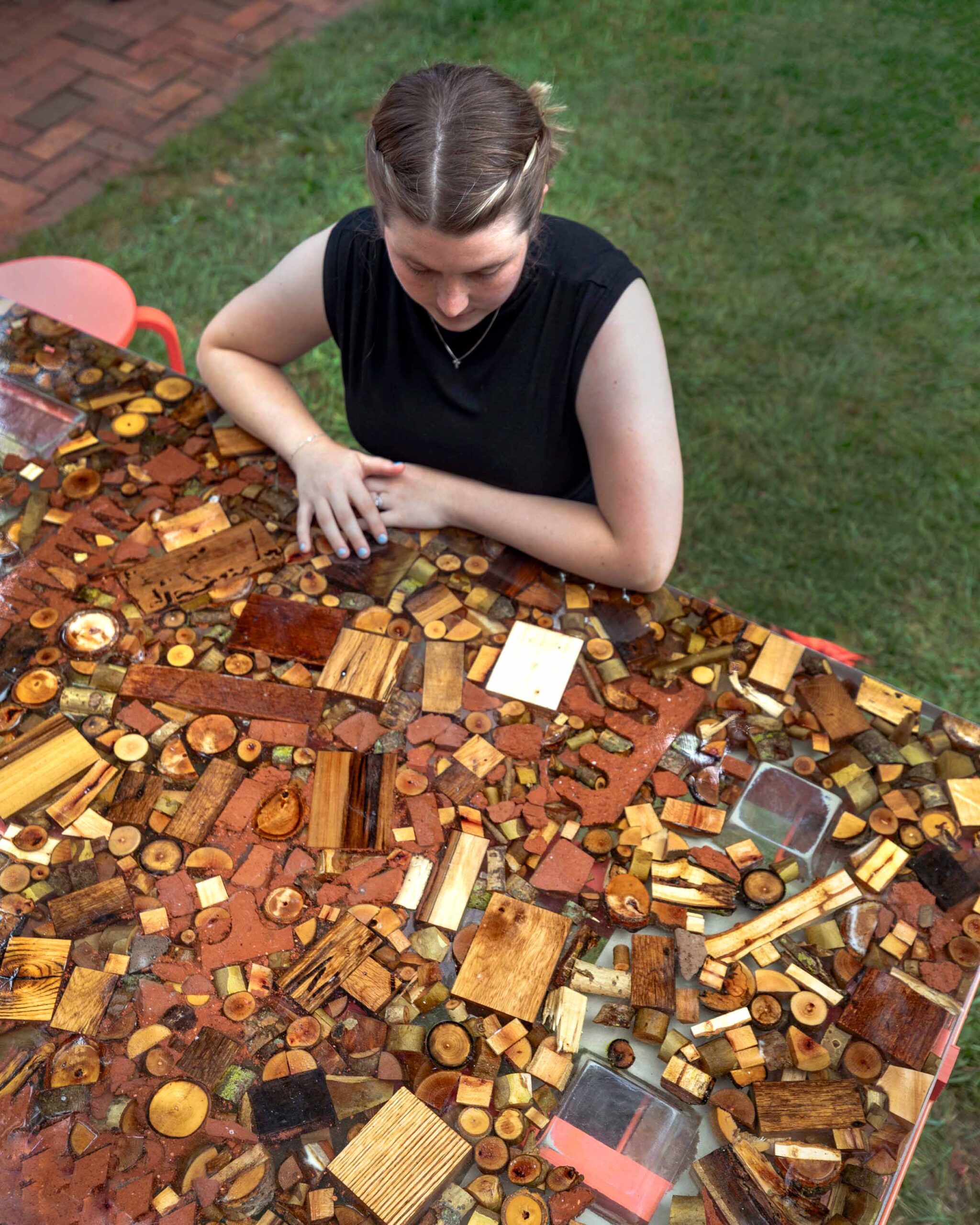
Riffing on scrapple, a Pennsylvania Dutch dish made with pork fragments, a 15-foot-long table consists of small pieces of wood, bricks, and other material bound with bioresin. Image credit: Hadley Fruits
The installation, which is titled Sylvan Scrapple, takes its name from scrapple, a breakfast dish that incorporates pork waste. There’s this parallel between thinking about how we use materials and thinking about how we use food, and then a prompt given to the public to engage with that narrative.
Sarah Wesseler: You’ve focused on wood and other bio-based materials in other projects. How does this installation relate to your larger body of work? What led you to look at this specific set of issues here?
MacDonald: Our larger mission as a practice is to reconsider the material palette that architects and builders use in light of the climate crisis. One of the challenges for architects is the role of specification: working with the materials available from manufacturers and allowed by building codes. Since we’re active in both practice and research, we consider how architects can play a bigger role in the building process, but also in material harvesting and processing. What opportunities emerge if we’re able to extend our role beyond specification?
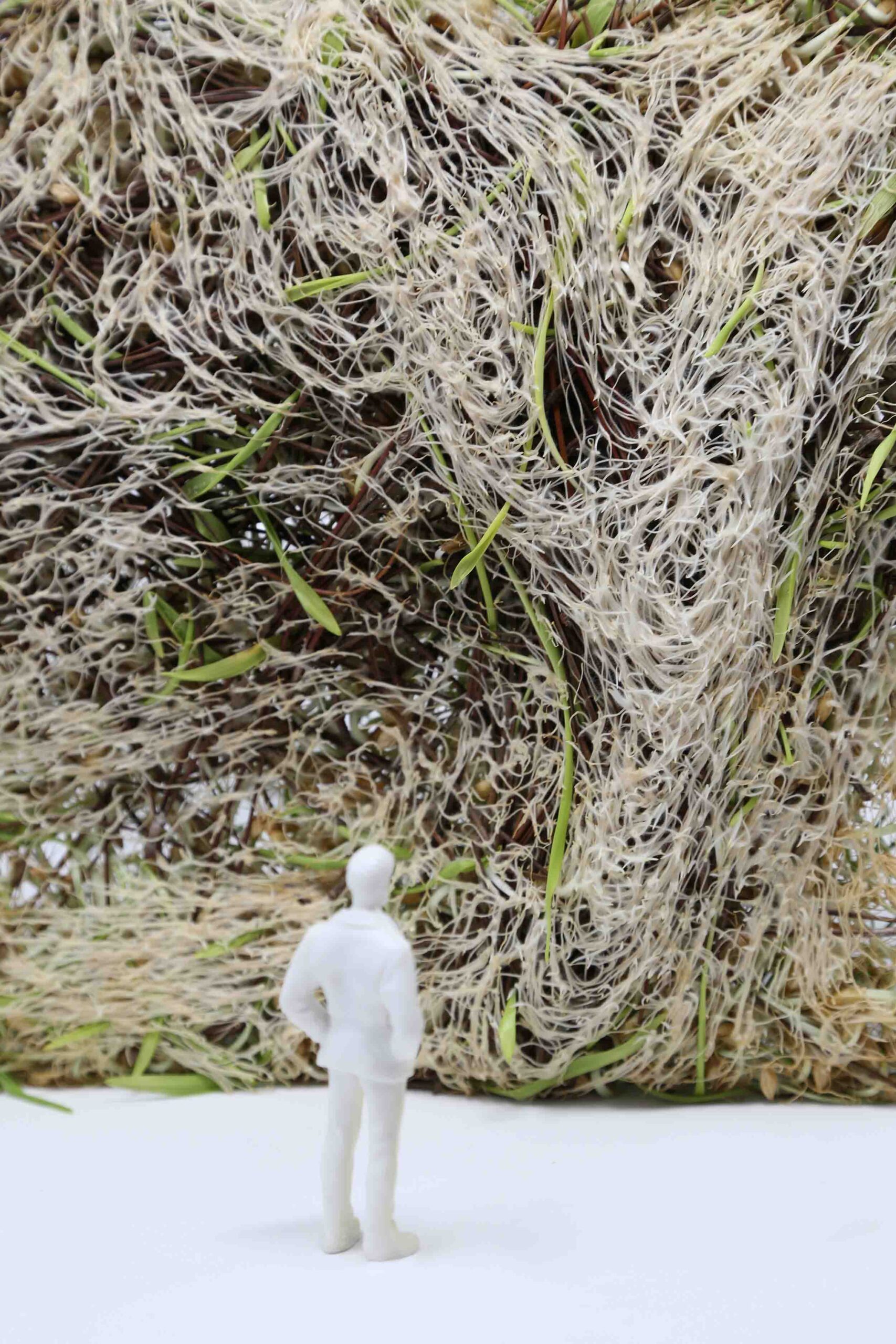
After Architecture’s Grown Models project experimented with molding barley seed into volumetric molds. Image credit: After Architecture
Schumann: We’re also thinking about using wood that is not conducive to conventional milling processes. Many trees are more curved or tapered, and there’s a lot of material waste when you reduce them into flat boards. So we’re using waste wood and parts of trees that might not be usable in conventional methods.
We’re also thinking about the afterlife of materials through the brick system in the project. We’re reauthoring the bricks that were salvaged from the Irwin Block: we’re water-jetting a number of them and splitting them with patterns, both to expand them, make them more porous when they’re stacked into the gabion wall system, but also to potentially add value to those bricks that now become designed objects that could take on other functions in the future. We’re working with various entities in Columbus to think about how those could be distributed after the installation closes. The idea is to add value to those materials so they don’t go to a landfill at the end of this temporary installation.
Carlisle: Can you say more about your collaboration with others at the university to process nonlinear wood? Is it possible to project some future uses for this technology?
Schumann: For a while now, we’ve been thinking about how we can use familiar materials in unfamiliar ways, and that often means that we have to actually build the tools that we use in our fabrication process.
This approach has taken a number of different forms. A couple of years ago, we produced what we called a “pillow forming” machine. That was essentially a robotic air mattress that served as a reusable formwork for casting different materials through a grid of inflatable pillows. The machine let us model a surface digitally, then basically hit some buttons and inflate the pillows to create a casting surface.
We have also wanted to work with wood in different ways and have found some challenges with existing technologies. Robotic systems are really productive and versatile, but also very expensive; not all people have access to them. CNC routing methods, on the other hand, are widespread and fairly accessible but also very time-intensive, and subtract through part reduction with a rotating bit, in turn producing a lot of material waste.
Our custom robotic sawmill design started with a seed grant through the University of Virginia, where we teach. We worked with Gavin Garner, who’s faculty in mechanical engineering, and Manuel Lerdau, who’s faculty in environmental science, looking at different material streams and existing systems. We began with a bandsaw sawmill and heavily modified it into a robotic system. We’re using that machine now for the first time to produce curved wood elements that are going into the wall system for Exhibit Columbus.
We have a long list of ideas of what to do with it in the future, starting with small prototypes or elements. We plan to produce curved or twisting lumber that will incorporate 3D scanning to respond to the geometry of input logs and address how such geometries might affect the forms of the resultant architecture.
When we begin these kinds of experimental investigations, we start by considering the relationship between material qualities and tools. This allows us to identify both challenges and opportunities of the specific material in question. Our goal is to produce designs that are co-authored or informed by material qualities. Once we determine a fabrication strategy, we begin by fabricating smaller elements, like columns or walls, to refine our approach, and then speculate on what larger assemblies might be possible. When we have the opportunity, we fabricate larger proofs of concept, like the wood walls for Columbus.
In the future, we hope to look at how this tool might be able to impact other kinds of existing systems, particularly within the mass timber world, including CLT: How might mass timber take on new architectural or structural possibilities if it’s not limited to using straight, flat, rectilinear lumber?
MacDonald: There are a couple of reasons why we want to work in this way. One is that timber represents a global material stream. Different species grow in different regions throughout the world, and the species that we use for construction represent a limited slice of the global supply. Wood offers great advantages in terms of being renewable, able to sequester carbon, and able to be decommissioned. So we’re trying to develop other ways to tap into a resource that is currently not fully utilized.
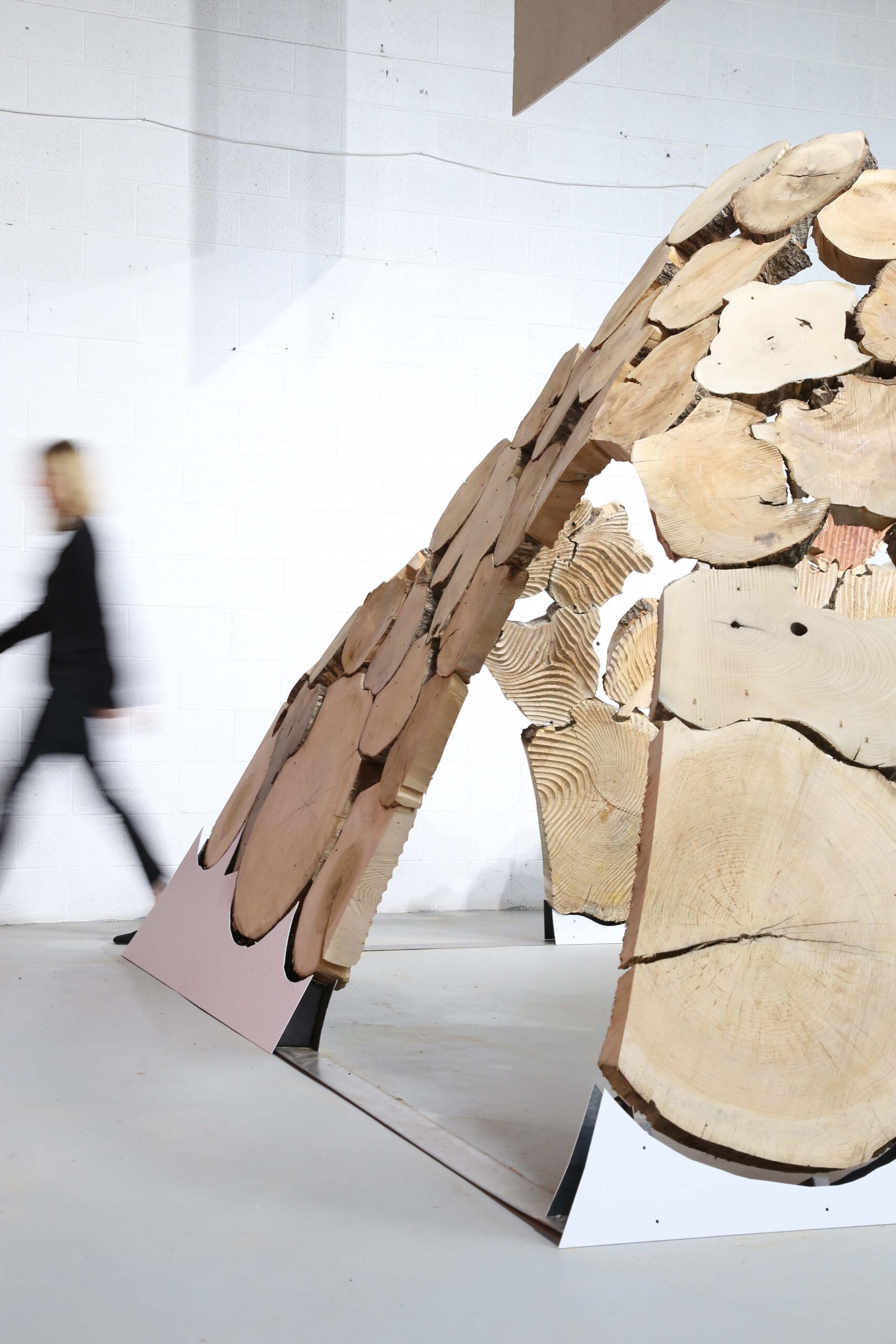
With the Tangential Timber pavilion, After Architecture developed a structural application for non-linear wood. Image credit: After Architecture
The second reason is a rethinking of how we leverage geometry and digital workflows today. In the early days of digital modeling and fabrication, new tools allowed architects to create complex forms out of standard materials. Some of the iconic early projects were characterized by plywood sheets cut into irregular shapes and waffled together. Building on that lineage, we see opportunities to leverage the complex geometries that already exist in material. Oftentimes, these geometries have performative qualities that are advantageous: curved geometries can create structure in different ways than flat geometries, for example.
Wesseler: To extend that thought further, can you tell us more about how you think about the potential of small projects like this installation to help build toward macro-level changes in the building sector?
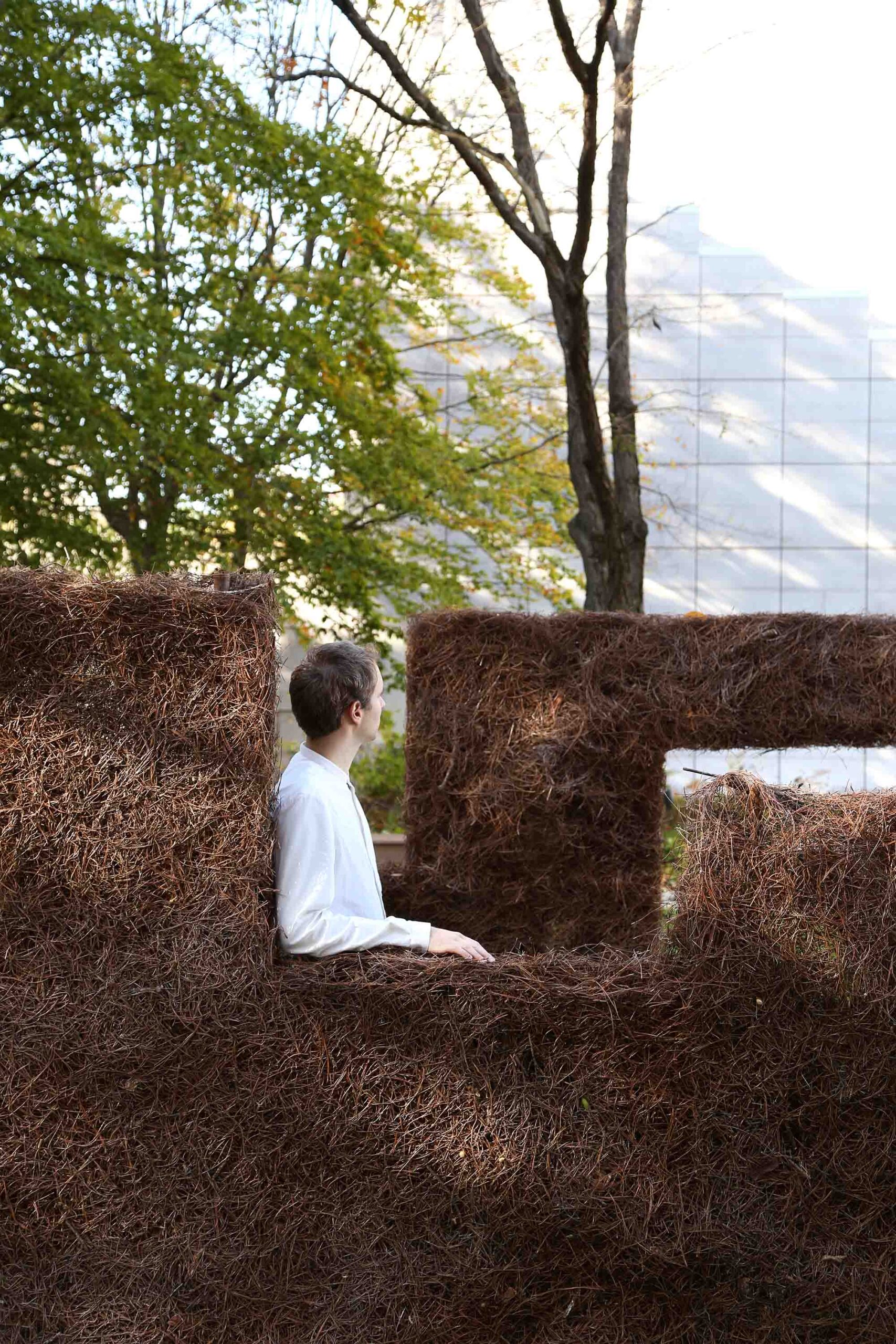
The practice’s Homegrown pavilion is constructed from small-scale landscaping waste and forestry waste joined together with a liquid bio-based binder. Image credit: After Architecture
Schumann: We have two different modes of operation. One is our practice, After Architecture, and the other is our academic research lab, the Before Building laboratory here at UVA. We’ve found that operating within academia, doing materials research, benefits our carbon reduction goals. Through research, we can take risks that might be irresponsible to do in practice, when we’re completing client-serving projects and need to adhere to existing building codes, processes, etc.
Having a foot in both worlds has been really interesting for us, and we hope that over the long term we can tackle some of the challenges of incorporating these fabrication methods and systems in practice. The primary barriers are policy and codification. We have to demonstrate that these things are possible and that they might be economically feasible or desirable, then go into a process of codification and testing to be able to prove the level of performance. We hope to do that going forward.
There are also issues around the public perception of these materials. To push this kind of work ahead we have to consider: What do people want? Is there a market for any of these things? What does the public think of them? Are designers going to want to use or specify these materials in their buildings? And how can you start to show how unfamiliar methods might be used with familiar materials?
That’s where built prototypes, even small-scale pavilion structures, come in. We find that creating something that the public or other designers can experience physically, or even view through photography, can go a really long way towards making progress on how these material systems are perceived across the public and profession.
Interview edited and condensed.
Explore
Lever Architecture lecture
The Portland, Oregon, firm is known for its ambitious use of cross-laminated timber.
Concrete, Reformed
Changing the way we use concrete could create broad-ranging benefits for society, says Tsz Yan Ng.
Getting Fit in the Anthropocene
In a new installation, Common Accounts considers attempts to perfect the self during an era of global environmental crisis.