Concrete, Reformed
Changing the way we use concrete could create broad-ranging benefits for society, says Tsz Yan Ng.
March 16, 2022
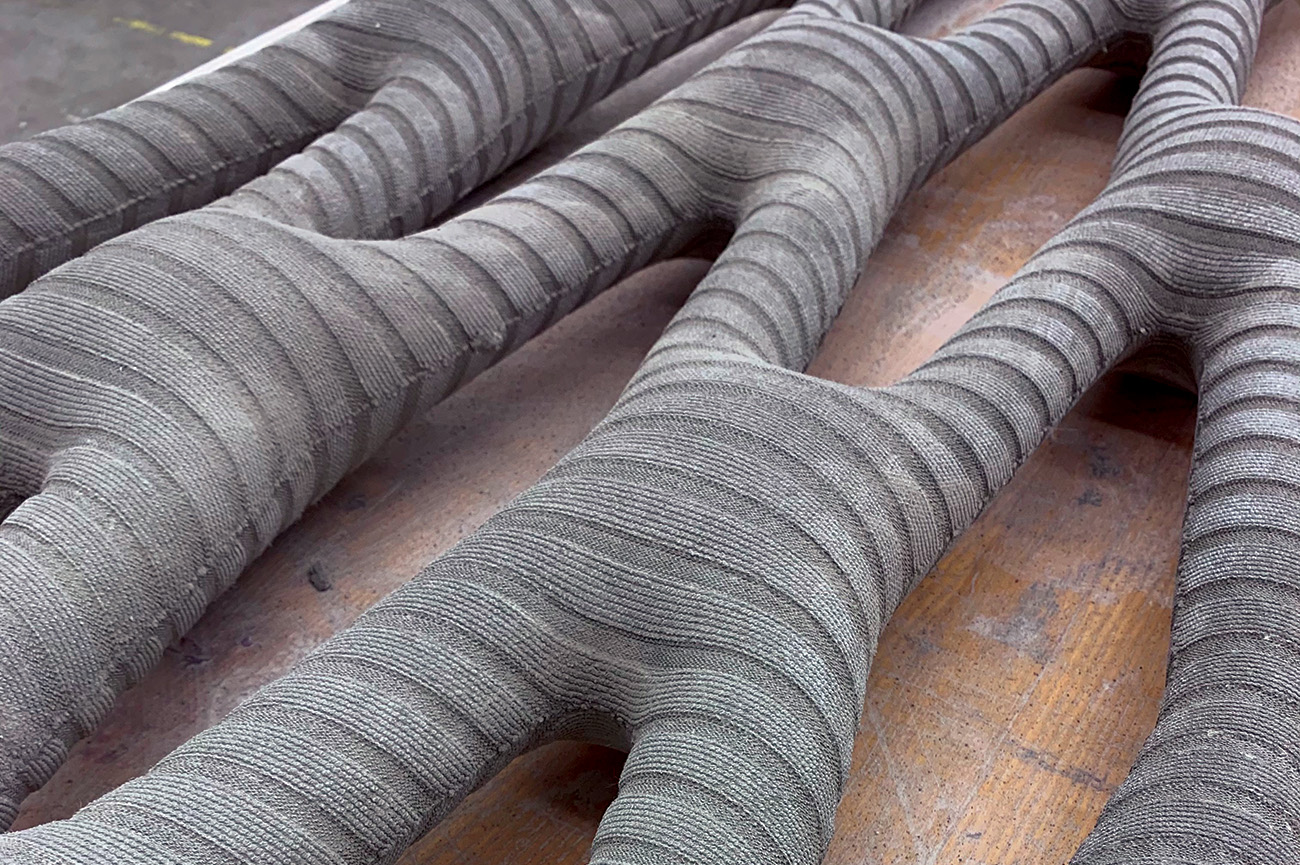
Image from Tsz Yan Ng's Knit Casting project, which examines the potential of CNC-manufactured fabric to create concrete formwork. Image credit: Tsz Yan Ng
In 2005, Tsz Yan Ng and Mehrdad Hadighi were commissioned to design an 11-story manufacturing building in Shantou, China, for fashion label Lafayette 148. Using the project as an opportunity to experiment with concrete construction, they developed a post-tensioning system that enabled a column-free extended floor span, as well as a cast concrete brise soleil (which they referred to as a “woven textile”) whose twisting form was engineered to draw light and air inward as part of a broader passive design strategy.
Left: Lafayette 148 building in Shantou, China. Right: Cast concrete brise soleil. Image credit: But-Sou Lai
For Ng, this project inspired a lasting fascination with concrete, which she now explores as an assistant professor at the University of Michigan’s Taubman College of Architecture & Urban Planning, a school known for materials research. Through a variety of investigations and collaborations, Ng considers how concrete can be reimagined to produce better environmental, social, and aesthetic outcomes.
The League’s Sarah Wesseler spoke with Ng about her work.
*
As architects have grown more concerned about concrete’s contributions to climate change, how do you see these conversations playing out in the materials community at Taubman College and beyond? How does embodied energy factor into your own research?
For my work on concrete, it’s a major issue. Concrete accounts for 8 percent of carbon emissions globally. It has such a bad rap. Since the Guardian published its Concrete Week series in 2019, everyone starts their presentation with what percentage of embodied emissions concrete accounts for and what we need to do about it. But in practice, we haven’t stopped using it. It’s still part of our building process. We still need it, especially in urban infrastructure.
So my work looks at incremental impact. Given how much concrete is used, if we can have an incremental impact, that would actually be huge. And it’s starting to happen, but it’s a long road.
One of the things I’m looking at is how to reduce the use of certain types of concrete in order to reduce material extraction and embodied energy. There’s been a lot of research and discussion with other colleagues at the university, not just within Taubman but with engineers, material scientists, etc. We’re trying to reach carbon negativity, not just carbon neutrality.
And it’s not just on the material side. We can think about developing different kinds of carbon sequestration in concrete—there are different developments along that front—but that alone won’t allow us to reach carbon negativity. What’s necessary is integration with design that addresses operational emissions.
My work is also trying to hybridize processes and material use for forming concrete. How do we reduce the formwork that is necessary to cast concrete, and how might other material systems come into play to help that? Can we reduce the amount of material that needs to be manufactured and delivered to job sites for formwork production, as well as the amount of construction waste that ends up in landfills once it’s removed?

Workers placing formwork for a concrete bridge in Switzerland in 2012. Image credit: Flickr user Kecko via Creative Commons 2.0
And from this, what kinds of new labor are necessary? It takes a lot of labor to make formwork, and that’s where the major costs go for concrete construction. If we can reduce the time, labor, and material required, that results in incredible savings for not just the contractor, but also for the consumer. We’re trying to leverage new technologies to understand how material systems could be manufactured in a more sustainable and efficient manner, which will ultimately lead to better building practices.
So it’s an entire ecosystem of innovation related to these material systems.
I’m wondering how these issues are being tackled outside of academia. Do you see the private sector devoting funding and resources to addressing similar questions? Have other organizations focused on creating the kind of multidisciplinary structures for collaboration that you’re describing?
This is something I’ve been looking at—the question of how new technologies are brought to industry and how they’re adopted. Generally, the way we build hasn’t changed much in the last 50 years. So how do we allow the building industry to be excited about these new methods of construction, new materials, and new designs and see the potential to adopt them?

Ng's Thermoplastic Concrete Casting project examined the potential of non-woven thermoplastic textiles to create molds for glass fiber reinforced concrete (GFRC), which is lighter and stronger than concrete typically used in construction. Standard processes for casting complex concrete surfaces—carving molds out of foam, for example—require significant investments of time, material, and labor. To reduce the amount of resources required, Ng and collaborator Wes McGee used tailoring and patterning, processes typically associated with clothing production, to create a heat-stiffened textile that could be used to cast GFRC chairs and an 11-foot-long wall with attached table. Image credit: Tsz Yan Ng
A lot of people need to be involved, definitely beyond just the university setting. This is something I’ve been trying to do more of for the last two years—reaching out to industries, working with other disciplines. There’s some federal funding available for this kind of work—the National Science Foundation has convergence research grants. When applying for this funding, it’s important to understand the multidisciplinary effort required to tackle certain big challenges.
But it’s hard to engage industry, because we have to develop the language to communicate with them, and also develop opportunities to see how new innovations could be deployed. For something like 3D printing, for instance, it’s extremely difficult. The testing needs to be in place so that builders are comfortable deploying the technology. The infrastructure of equipment has to be in place, along with the specialized skills needed to operate it.
So it’s a long, multi-part process. I borrow from industries like industrial design to understand this type of work as R&D—what we can now think of as architectural R&D. In the R&D space, we have material systems we need to figure out, and we’ve got to work with engineers and scientists. That research might include fundamental science, but as designers, we’re also thinking about applied research. The process looks at what kind of new technologies are necessary for a new material; how those are integrated; what kind of new building typologies and systems are developed so that projects meet certain performance criteria; and then, finally, how we engage industry so that they adopt these technologies and systems. All these different players need to be involved.
Architectural R&D is not really funded in the US, but other countries invest heavily in it. The Japanese government, for instance, funds R&D labs in the construction industry. In the US, there’s a huge separation between the private sector and the research and development community, and the funding is not typically envisioned as clearly in terms of bringing these realms together. But there is a McKinsey report that talks about how R&D is beneficial for everyone; it’s a win/win situation, and not just in the building sector.
So for architecture in particular, because it is such a major manufacturing endeavor involving an incredibly large workforce—not to mention just the GDP alone for construction—how do we address this ecosystem so that it will work for everyone?
As my work matures and I’m trying to develop the language to engage developers, builders, and the industry in general, I think a lot about the fact that this engagement is work in and of itself. Architects want to design; we want to build beautiful things. What I’m describing—the behind-the-scenes work, the R&D, the relationship-building—that’s not the sexy part of architecture. It’s not sellable. But I hope that more attention will be paid toward this type of work, and hopefully that will allow architectural R&D to have a push in the US.
Right, and the need for that kind of push becomes even more apparent when you consider the speed and scale of the changes required to minimize the impacts of climate change. When you talk to people in industry, do you find that they’re interested in collaborating with people outside their companies to develop new ways of building?
A lot of industries are reaching out to research labs now because they know that that’s where the latest innovations are happening, and I think there’s starting to be more collaboration. I have seen more people reaching out to me. It’s super interesting that everyone is trying to understand whether there could be hybrid systems for construction that could provide an easier way for new technologies to be adopted.
I do think the industry is looking for alternative processes of building right now because there is such a huge labor shortage. And this shortage is probably only going to get worse in the future. A lot of that labor is unskilled; people don’t want to do the difficult work onsite. It’s physically exhausting, and a lot of it is dangerous. So might this be a moment when automation technology steps in to try to address that particular kind of labor shortage: the labor that people don’t like doing?
I’m thinking about automation as something that’s not trying to take away jobs, but instead reimagine them. There are also opportunities for different skills to be inserted so that it’s not such a binary division between unskilled and skilled labor. In addition to making construction safer, I think this could help the workforce acquire different skills and see a different kind of value in its work.
Could you say more about how you think about questions of labor in your research into concrete specifically?
The material systems I work with most are concrete and textiles. Those two materials sometimes work together, especially for forming. An easy way to think about my research is that the processes I look at are very labor-intensive in their current forms—I’m seeking ways to make them less labor-intensive, but also reduce climate impacts and insert design opportunities.
For one of my projects, I’m working with a colleague at Taubman, Sean Ahlquist, who specializes in CNC knitting. Clothes can be made with CNC knitting, but for this project we’re trying to really tune the material, employing what we call functional grading so that, for instance, a continuous piece of material can have different performance across that material. We’re looking at how we can use this technology to make formwork for casting concrete.
A piece of polyester knit has far lower carbon emissions than heavy, rigid formwork. And soft formwork is packable; you can send it anywhere to deploy for casting. But it can also enable complex geometries that are quite difficult to do with traditional casting processes—imagine that concrete is filling a bag. But how do you control that? We’re looking into these issues, trying to figure out all the different processes required to achieve the desired final outcome of the concrete components.

Ng's Knit Casting project creates CNC-knitted formwork for casting GFRC, exploring the potential to enable complex geometries and eliminate the need for molding materials such as wood or foam, thereby reducing production time and construction waste. Collaborating with Sean Alhquist and Evgueni T. Filipov, Ng experimented with four different typologies: diagrid, drupelet, aperture, and 3D funnel shell. Images courtesy Tsz Yan Ng Design
You said that concrete probably isn’t going to go away, and that given how much of it is used, even incremental change could add up to significant emissions reductions. Stepping back a bit further, where do you see a positive trajectory for concrete over the next few decades? If it’s not likely that we’ll stop using it altogether, how do you think we can use it most effectively?
So there are a lot of crises happening today, and the way we build has to address what these crises are pointing to. The housing crisis is a major one. I’m working with other researchers on addressing this: the idea that 70.7 million people will move to urban areas in the US by 2050, according to the United Nations, and we have no housing for them. There’s a housing shortage right now that is partly a result of the 2008 subprime mortgage crisis, because the builders stopped building at that time. It’s a supply and demand issue, but suddenly we have a supply chain and labor shortage crisis exacerbating the situation.
But instead of addressing this issue by just building more homes, we also have to understand it in terms of sustainability. I don’t know how long we can continue to build sprawl in the US. Certainly, during this pandemic time, people tend to want more space and more outdoor space, but I’m not so sure sprawling single-family homes are the answer—maybe we need to redesign multi-unit housing so that people’s needs are addressed. Also because if you’re living out in the suburbs you have to drive into work, which adds to emissions.
So it’s a complex system, and there are a lot of interesting projects looking at how concrete could be used to address some of these issues.
I’m working on a project with another collaborator, Wes McGee, looking at the potential to 3D print with a concrete called ECC (engineered cementitious composites) developed by our colleague at the University of Michigan’s college of engineering, Dr. Victor Li. ECC is a fiber-reinforced material known as bendable concrete; you can literally bend it. And what’s amazing about this material, too, is that it’s self-healing; these micro-cracks actually self-heal with mineral carbonization. So we’re using this for 3D printing.
There’s a lot of 3D printing out there. A lot of people are 3D printing single-family homes, but that material isn’t reinforced, so there’s a limit of how far they can build: typically one or maximum two stories. Since ECC is stronger and more resilient, we think we can perhaps build higher than two stories. Using this material, we can print components that are just as strong as typical concrete, but use less material. We can deposit the material where it is needed most in the component.
There’s also industrial waste such as fly ash that can be used to replace cement [the most carbon-intensive ingredient in concrete]. So from a material point of view, there are a lot of opportunities to reduce emissions for concrete construction.
Linking that with what we are designing and building, we can address societal needs such as the housing crisis. Rather than building single-family homes, we could build multi-unit homes that take up less footprint in our built environment. So it’s not just the material, or the technology of 3D printing, but also integrating design solutions for how such technology could be deployed most effectively.
Another key aspect to think about with these innovations is cost. New technology shouldn’t be just for privileged people who can afford to pay more for it, right? Some companies are looking at ways to connect new technologies like 3D printing to cheaper ways to build, trying to create more affordable homes for people in different segments of society.
So definitely, the question of how we use concrete for building in the next 30 years is really important. We have to think about, who is this concrete for? How is it being used? And how do we change an industry that has been doing the same thing for the last 50-plus years?
Interview edited and condensed.
Explore
FF – Distance Edition: Rael San Fratello
Gather round the hearth in Rael San Fratello's Casa Covida, a house made from 3D-printed mud.
Carrots, Sticks, and Low-Carbon Buildings
To help designers take on global warming, we need to think about psychology, not just technology, says Arup's Fiona Cousins.
Alan Organschi: Building a global carbon sink
Large-scale engineered wood products offer the possibility of turning cities into carbon sinks, Organschi posits.